Композитные отливки для коксохимической промышленности

В данной работе рассматриваются вопросы, связанные с технологией получения составных отливок, состоящих из двух частей: рабочего слоя и опорной части, выполненных из высокохромистой стали марки X46Cr13 и серого чугуна марки EN-GJL-HB 255 соответственно, в системе жидкость–твердое тело путем предварительной установки монолитной вставки в полость формы. В рамках исследований выявлен и описан механизм образования переходных зон в зоне соединения двух вышеуказанных сплавов. Показано, что явлением, определяющим образование постоянной связи между соединяемыми материалами, является перенос С и тепла от «высокоуглеродистого и горячего» материала опорной части, залитого в форму в виде жидкого чугуна, к «низкоуглеродистому и холодному» материалу рабочего слоя, размещенного в виде стальной монолитной вставки внутри полости формы. В работе также рассматривается пригодность разработанной технологии получения составных отливок для использования в коксохимической промышленности. Разработанные для футеровки коксовозных вагонов полноразмерные литые плиты из высокохромистой стали и серого чугуна прошли положительную проверку в реальных условиях эксплуатации коксохимического завода.
Введение
В последние годы в различных отраслях промышленности возрастает спрос на отливки специального назначения, в том числе обладающие высокой твердостью, высокой стойкостью к абразивному износу, коррозионной стойкостью при комнатной и повышенной температуре. Такие детали часто изготавливаются полностью из дорогостоящих и дефицитных материалов, например, из высоколегированных сталей и литейных сталей, сплавов с матрицами Ni или Ti и др. Во многих случаях это излишне, поскольку высокие эксплуатационные свойства часто требуются не от всей отливки, а только от ее рабочей поверхности. В таких случаях условия эксплуатации отливки приводят к износу только одной поверхности, так называемой рабочей поверхности, что приводит к превышению ее допустимого допуска на размер и вынуждает всю отливку отправлять в брак, что с учетом использования дорогостоящих материалов можно считать неэкономичным.
Учитывая вышеперечисленные факторы, технология составного литья приобретает особое значение. Она может быть использована в тех случаях, когда, как описано выше, критерий высоких эксплуатационных свойств требуется только для наружного рабочего слоя отливки, а остальная ее часть играет лишь роль несущей конструкции, не подвергаясь непосредственному воздействию факторов, приводящих, например, к коррозионному или абразивному износу. Кроме того, данная технология является одним из наиболее экономичных способов улучшения рабочей поверхности отливок , поскольку позволяет изготавливать составные детали непосредственно в процессе их изготовления. В результате для массивных отливок с простой геометрией она может стать существенной технологической альтернативой обычно применяемым наплавкам и термическому напылению или поверхностной термообработке. Кроме того, применение технологии литья под давлением, помимо ее экономических преимуществ, в отличие от вышеперечисленных технологий наплавки и поверхностной термообработки, не сопряжено с опасностью образования трещин в околошовной зоне, возникающей при использовании вышеперечисленных методов.
Изготовление сложных отливок, состоящих из двух основных компонентов: рабочей части (слоя) и опорной части, называемых также биметаллическими отливками, осуществляется, как правило, по трем основным технологиям, учитывающим агрегатное состояние, в котором находятся материалы в момент соединения, т.е. в следующих системах:
• жидкость–жидкость; • твердое–твердое ; • жидкость–твердое тело.
Для первой упомянутой технологии обе биметаллические детали состоят из материалов, изготовленных исключительно литьем. Примером этой технологии является технология, в которой изготавливаются две независимые литниковые системы, гарантирующие двухэтапное заполнение полости песчаной формы. Согласно этому способу изготовления, биметаллические элементы молота, футеровки шаровых мельниц или валков отливаются в материальных конфигурациях рабочего слоя из хромистого чугуна с опорной частью из низкоуглеродистой литой стали.
Напротив, в технологии «твердое тело – твердое тело» можно склеивать ранее полученные литые сплавы, например, серый чугун с пластинчатым графитом с чугуном с шаровидным графитом или литые сплавы, с нелитыми сплавами, например, хромистый чугун с углеродистой сталью. Более того, с помощью этой технологии можно получить склеивание между двумя сталями, например, углеродистой сталью и нержавеющей сталью, как представлено в статье. Технология «твердое тело – твердое тело» ограничена небольшими элементами с максимальной поверхностью контакта между обоими компонентами приблизительно 200 мм2 и толщиной 30 мм. Кроме того, эта технология требует повышенной температуры приблизительно 1000 °C, давления во время склеивания 1–10 МПа и вакуума во время создания склеивания.
Между тем, технология «жидкость-твердое тело» может использовать комбинацию литых и нелитых сплавов. При этом способе изготовления элемент, обогащающий поверхность отливки, помещается в форму в виде гранулированной или монолитной вставки непосредственно перед заливкой расплавленного сплава. При использовании гранулированных вставок производились составные отливки в конфигурации материала рабочий поверхностный слой из WC , Al2O3 или SiC [ 12 ] с нелегированной литой сталью или несущей частью из серого чугуна. Этот тип составного литья характеризуется твердым рабочим поверхностным слоем, устойчивым к абразивному износу, что является решающим фактором его применимости в горнодобывающей промышленности. Примером технологии с использованием монолитной вставки являются составные отливки в конфигурации, которая включает твердый и стойкий к абразивному износу хромистый чугун, соединенный с привариваемой низкоуглеродистой стальной пластиной. Примеры небольших тестовых отливок, изготовленных с использованием монолитных вставок из высокохромистой или хромоникелевой нержавеющей стали с использованием технологии «жидкость-твердое тело» с серым чугуном, представлены в работах. Возможно использование 3D-печатных элементов в качестве монолитных вставок, что было показано в работе при составном литье в конфигурации чистого Ti с серым чугуном.
Другое разделение можно провести, рассмотрев характер связи обеих биметаллических деталей. Она может быть диффузионной, адгезионной или механической. Учитывая прочность связи и способность рассеивать тепло, а следовательно, и срок службы составной отливки, наиболее выгодной, очевидно, является диффузионная связь, характерной особенностью которой является образование меньшей или большей переходной зоны в результате физико-химических явлений, происходящих на границе слоев: рабочий слой – опорная деталь. Однако для адгезионной связи, образованной в результате взаимного межмолекулярного притяжения, явление диффузии не происходит. С другой стороны, для получения механической связи с использованием технологии жидкость – твердое тело необходимо сделать надрезы, выступы или крючки в отлитой детали, чтобы соединить ее с деталью, образованной после затвердевания жидкого сплава, залитого в форму. Это решение использует механическую связь, образованную явлением усадки литья, которое происходит в отлитой детали, как представлено в работах.
В результате в статье представлены результаты исследований технологии литья составных отливок в системе жидкость–твердое тело, основанной на способе подготовки полости формы путем предварительной установки монолитной вставки из высокохромистой стальной плиты, залитой серым чугуном, целью которых была разработка совершенно новой и ранее не описанной в литературе технологически полезной биметаллической плиты для использования в футеровке коксотушильного вагона. Кроме того, исследования направлены на описание механизма связи в анализируемых составных отливках, в которых улучшение абразивной износостойкости достигается за счет применения высокохромистой стали и, как следствие, создания твердой микроструктуры, содержащей карбиды Cr(Fe) в мартенситной матрице, с одновременным улучшением коррозионной стойкости, т.е. жаропрочности и стойкости к коррозионному воздействию охлаждающей воды, что достигается за счет создания пассивного поверхностного слоя с оксидами Cr.
Материалы и методы
В соответствии с целью статьи, в общем случае коксотушильный вагон футерован 376 плитами следующих размеров: ширина 520 мм, длина 575 мм, толщина 25 мм. Они используются в цикле производства кокса, включающем следующие этапы: • Выгрузка из коксовой батареи в тушильный вагон от нескольких до десяти и более тонн кокса, нагретого до 900–1100 °C, с высоты от 2 до 4 м ( рисунок 1 а), • Перевозка нагретого кокса в тушильную башню ( рисунок 1 б), • Тушение кокса сухим способом с нейтральными газами или мокрым способом с использованием воды, протекающей по замкнутому контуру, содержащей большое количество вредных загрязняющих веществ, ускоряющих коррозию ( рисунок 1 в, г), • Сброс охлажденного кокса с поверхности тушильного вагона на желоб, откуда он транспортируется на сортировочный завод.
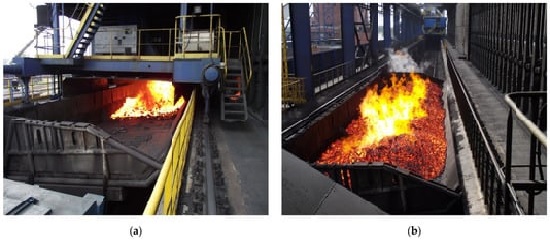
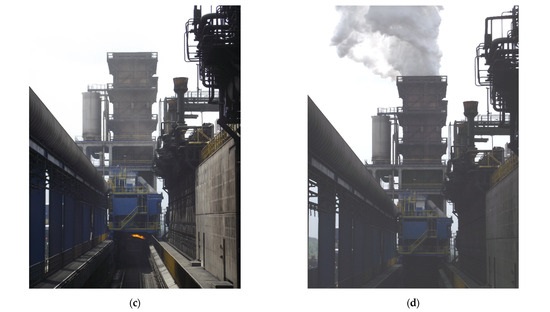
Рисунок 1. Вид технологического цикла производства кокса: выгрузка нагретого кокса, выталкиваемого из коксовой батареи, на поверхность тушильного вагона ( а ), транспортировка нагретого кокса от места выгрузки в тушильную башню ( б ) и вагон в тушильной башне ( в ) с последующим процессом мокрого тушения кокса ( г ).
Представленный выше цикл производства кокса осуществляется от 50 до 150 раз в сутки, что приводит к воздействию на футеровочные плиты вагонов закалки высоких температур, термоударов, коррозионного воздействия охлаждающей воды и абразивного износа в системе металл-кокс. В результате возникает проблема неудовлетворительного срока службы плит из крапчатого чугуна EN-GJN-HB 340 с добавкой Cr ≤ 2 мас.%, используемых для футеровочных плит ( рисунок 2 ). Такой чугун обеспечивает срок службы футеровочных плит, не превышающий примерно 50% от общего срока службы, предусмотренного для вагона закалки. Однако из-за трудностей, возникающих при демонтаже сильно корродированных винтовых соединений, крепящих футеровочные плиты к поверхности вагона, и вызванных этим простоев, допускается, несмотря на повреждения, их дальнейшая эксплуатация, что одновременно создает условия, способствующие коррозионному разрушению остальной конструкции вагона.
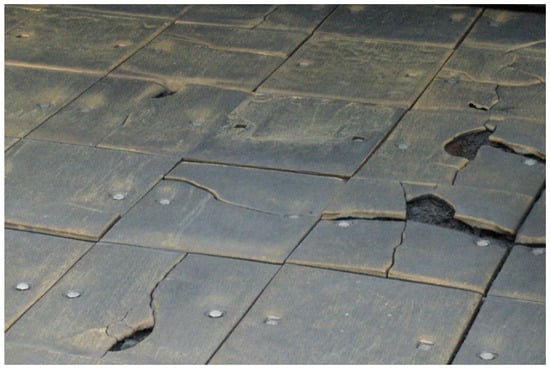
Рисунок 2. Вид поврежденных чугунных литейных плит, используемых в качестве футеровки коксотушильного вагона, все еще эксплуатируемого, несмотря на разрушение.
В рамках проведенного и представленного эксперимента были выполнены составные отливки по следующей методике: разработан тип и устройство литниковой системы литья с использованием системы жидкость-твердое с монолитной вставкой из стали X46Cr13 ( таблица 1 ) толщиной 5 мм (твердый/рабочий слой литья), залитой серым чугуном (жидкость/опорная часть литья) марки EN-GJL-HB 255 ( таблица 1 ). Далее была изготовлена деревянная модель литья, разделенная на рабочий слой и опорную часть с размерами составной литейной плиты, используемой для футеровки коксового вагона: ширина 520 мм, длина 575 мм и толщина 25 мм, и изготовлена двухсоставная форма из классического формовочного песка с кварцевой матрицей с бентонитом в качестве связующего, с плоскостью раздела, соответствующей поверхности контакта рабочего слоя с опорной частью. Затем форма была высушена при температуре 180 °C. Затем поверхность контакта монолитной вставки была подготовлена путем пескоструйной обработки и покрыта флюсово -водным раствором Na2B4O7 и H3BO3 , затем высушена при температуре 120 °C в течение 1 часа для удаления H2O . Наконец , форма была разобрана , и ранее подготовленная монолитная вставка была помещена в ее полость ( рисунок 3 ).
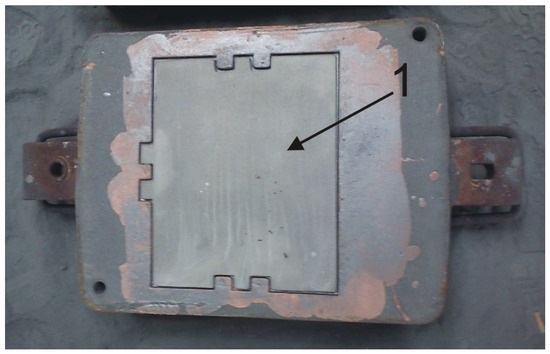
Рисунок 3. Вид песчаной формы с размещенной внутри ее полости монолитной вставкой из стальной пластины X46Cr13 (1).
На следующем этапе была собрана и подготовлена форма для заливки жидким чугуном. Затем была подготовлена металлошихта, что позволило получить серый чугун EN-GJL-HB 255 с пластинчатым графитом в перлитной матрице. После этого был проверен химический состав жидкого сплава и при необходимости скорректирован после расплавления металлошихты. Согласно представленной методике были проведены отливки 8 составных литейных плит; 4 формы были залиты жидким чугуном при температуре 1450 °C, а 4 — при температуре 1550 °C. Во всех 8 случаях температура монолитной вставки внутри формы перед ее заполнением составляла около 20 °C. Для каждой опытной отливки в ее форме после заливки применялось свободное воздушное охлаждение. После охлаждения отливка выбивалась из формы и удалялись элементы литниковой системы. На следующем этапе проводилась оценка качества отливки составной плиты путем визуального осмотра и неразрушающего ультразвукового контроля зоны соединения рабочего слоя с опорной частью. Испытания проводились с использованием дефектоскопа DIO 1000 STARMANS ELECTRONICS (STARMANS ELECTRONICS SRO, Прага, Чешская Республика) с плоской головкой PN10-4C, при этом зоной, показывающей надлежащее, постоянное соединение рабочего слоя с опорной частью, считалась зона, где нижний эхосигнал был выше эхосигнала переходной зоны (головка прикладывалась со стороны рабочего слоя (стальной пластины)).
Объем лабораторных испытаний включал в себя, на образцах, вырезанных из центра составной отливки, тестирование химического состава стали X46Cr13 и серого чугуна с использованием спектрометра тлеющего разряда LECO GDS500A (LECO Corporation, Сент-Джозеф, Мичиган, США). Кроме того, в случае определения C в сером чугуне использовался ИК-анализатор (инфракрасная спектроскопия) LECO CS-125 (LECO Corporation, Сент-Джозеф, Мичиган, США). Кроме того, для образцов, вырезанных из центра отливки, были проведены металлографические испытания с использованием оптического микроскопа NIKON Eclipse LV150N (NIKON Metrology Europe NV, Лёвен, Бельгия) (LOM), сканирующего электронного микроскопа (СЭМ) INSPECT F (FEI Technologies Inc., Хиллсборо, штат Орегон, США) с энергорентгенодисперсионным спектрометром (EDS) и просвечивающего электронного микроскопа (ПЭМ) FEI TITAN 80–300 (FEI Technologies Inc.,
Хиллсборо, штат Орегон, США). Образцы для LOM и SEM-тестирования были подготовлены путем резки, шлифовки и полировки с использованием водной суспензии Al2O3 и электролитического травления с использованием LectroPol-5 STRUERS (STRUERS ApS, Ballerup, Дания) и реагента следующего химического состава: 3 г FeCl3 + 10 см3 HCl + 90 см3 C2H5OH , при напряжении 15 В и времени 15 с. Образцы для TEM-тестирования были получены с использованием системы FEI FIB Quanta 200i (FEI Technologies Inc., Hillsboro, OR, USA ) , которая позволила собрать ламели размерами 20 × 8 мкм и толщиной 50 нм с использованием сходящегося пучка ионов галлия из SEM-изображений. Металлографические испытания были дополнены измерениями микротвердости в трех точках для каждой зоны микроструктуры (расстояние между точками составляло 2 мм) с использованием твердомера Виккерса с помощью твердомера FUTURE-TECH FM 700 (FUTURE-TECH CORP., Фудзисаки, Япония) и алмазного индентора (прямая четырехугольная пирамида с углом при вершине 136°), нагруженного усилием 4,9 Н (μHV 0,5). Измерения твердости поверхности в девяти точках, распределенных на образцах, вырезанных из центральной, половинной и прикраевой областей рабочего слоя (три точки измерения на образец), проводились по методу Виккерса с помощью универсального твердомера SUNPOC SBRV-100 D (Guizhou Sunpoc Tech Industry Co., Ltd., Гуйян, Китай) и алмазного индентора (прямая четырехугольная пирамида с углом при вершине 136°), нагруженного усилием 50 Н (HV5).
Для определения пригодности для промышленного применения, т.е. для использования изготовленных в установке составных литых плит в качестве футеровки коксовозного вагона, рабочей поверхности из высокохромистой легированной стали X46Cr13 и опорной части из серого чугуна EN-GJL-HB 255, был проведен ряд испытаний, охватывающих следующие виды деятельности:
• Установка 3 составных литейных плит и 3 контрольных плит из чугуна, соединенных с низколегированным крапчатым чугуном EN-GJN-HB 340 со средней твердостью поверхности 350HV5 в коксотушильном вагоне ( рисунок 4 ), • Использование листового литья в условиях работы коксотушильного вагона ( рисунок 5 ), включающего от 72 до 81 цикла получения кокса (выгрузка, транспортировка, мокрое тушение и сброс кокса в желоб) в сутки, 7 дней в неделю, • Демонтаж отливок плит после завершения примерно 18 500 циклов производства кокса в течение 8 месяцев.
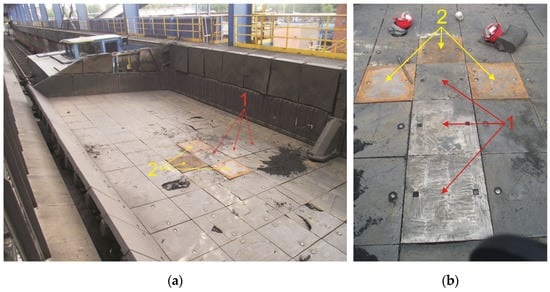
Рисунок 4. Установка 3-х полноразмерных составных отливок рабочего слоя из легированной стали X46Cr13 с опорной частью из EN-GJL-HB 255 (1) в коксотушильную машину и 3-х контрольных плит из крапчатого чугуна EN-GJN-HB 340 (2): ( а ) общий вид и ( б ) детальный вид.
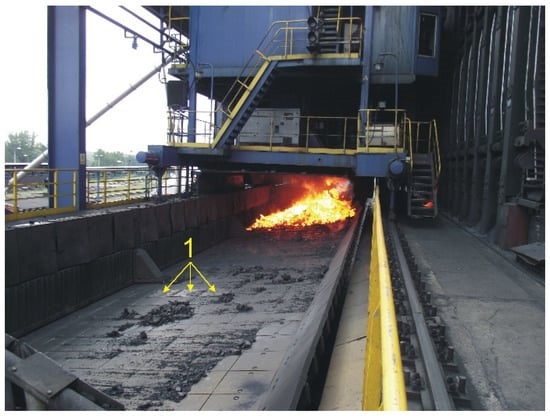
Рисунок 5. Вид отливок листового состава рабочего слоя из легированной стали X46Cr13 с опорной частью из серого чугуна EN-GJL-HB 255 (1) при работе коксотушильного вагона. В свою очередь, объем промышленных испытаний включал в себя следующее: • Объемные потери путем измерения толщины с точностью до 0,1 мм и потери веса путем измерения массы с точностью до 0,1 кг составных пластин в условиях эксплуатации коксотушильного вагона и сравнение результатов с повреждениями однородных плит из крапчатого чугуна EN-GJN-HB 340 ( таблица 1 ), эксплуатируемых в тех же условиях, • Испытание микроструктуры пластин составного литья после эксплуатации с использованием LOM (образцы, вырезанные из центра составного литья), • Испытания твердости после эксплуатации отливки из составного сплава по вышеизложенной методике с использованием метода Виккерса.
Результаты и обсуждение
На рис. 6 а, б представлен вид примера составной литой пластины в следующем расположении: рабочий слой из легированной стали X46Cr13 и опорная часть из серого чугуна EN-GJL-HB 255. Проведенные неразрушающие ультразвуковые испытания показывают, что для составных литейных пластин, отлитых при температуре 1450 °C ± 10 °C, получена постоянная связь высокохромистой стали с серым чугуном в пределах площади контактной поверхности в диапазоне примерно от 60% до 80%. В результате эти четыре составные отливки были признаны технологически бесполезными. Однако при температуре заливки 1550 °C ± 10 °C была достигнута постоянная связь обоих материалов компонентов, покрывающая всю контактную поверхность. Поэтому остальные представленные здесь испытания относятся только к этим составным литейным пластинам. Постоянная связь внутри составной литейной пластины подтверждает макроструктуру поперечного сечения, пример которой, вырезанный из центра биметалла, представлен на рис. 6 в.
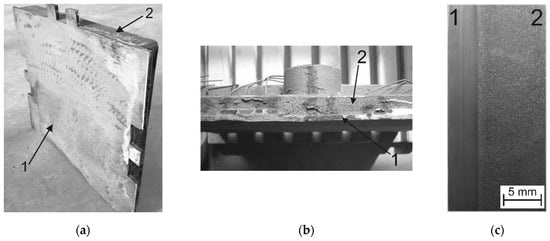
Рисунок 6. Вид составной литой пластины примера системы сталь X46Cr 13 (1) и серый чугун EN-GJL-HB 255 (2): ( а ) общий вид, ( б ) вид сбоку, ( в ) фрагмент макроскопического поперечного сечения.
В свою очередь, на рисунке 7 представлена микроструктура зоны соединения внутри составной литой пластины. Структура зоны соединения биметалла формируется в результате диффузии, прежде всего С в направлении от опорной части к рабочей и охлаждения от высокой температуры, до которой нагревается монолитная вставка, и источником которой является жидкий чугун, заливаемый в форму.
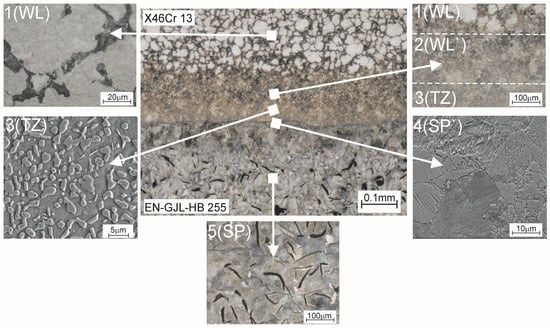
Рисунок 7. Микроструктура зоны соединения в составе отливки в системе: рабочий слой из стали X46Cr13 с опорной частью из серого чугуна EN-GJL-HB 255.
В целом в зоне соединения стали X46Cr13 с серым чугуном можно выделить две классические зоны с точки зрения микроструктуры, типичной для связанных материалов, а именно зону 1(WL), соответствующую микроструктуре X46Cr13, и зону 5(SP), соответствующую микроструктуре серого чугуна. Зона зоны 1(WL) из-за удаленности от чугунной детали не цементируется, а лишь нагревается до высокой температуры, составляющей от примерно 1000 до примерно 1150 °C, как показано в работе другого автора. Следует отметить, что указанная температура вставки в зоне 1(WL), т.е. именно на участке от поверхностного слоя биметалла до границы с зоной 2(WL`) (микроструктура которой формируется в результате как высокой температуры, так и цементации), находится в диапазоне, характерном для температуры аустенизации, используемой в классических процессах термической обработки легированной стали X46Cr13. Таким образом, для легированной стали X46Cr13, проявляющей явление самозакалки, нагрев до температуры фазовой стабильности γ в сочетании с охлаждением в песчаной форме со средней скоростью около 0,1 °C/с привел к получению микроструктуры рабочей части, отличной от исходного состояния до заливки формы, т. е. исходная микроструктура, состоящая из карбидов Cr(Fe) 23C6 в ферритной матрице (рисунок 8а), твердостью 200 μHV0,5, трансформируется в конечную микроструктуру, состоящую из карбидов Cr(Fe)23C6 в мартенситно - перлитной матрице ( рисунок 8б ) , твердостью 460 μHV0,5 ( рисунок 9 ). Фазовый состав представленных микроструктур стали X46Cr13 в различных состояниях типичен, что подробно описано в работах. В свою очередь, зона 5(SP) имеет микроструктуру, типичную для серого чугуна EN-GJL-HB255, т.е. пластинчатый графит в перлитной матрице.
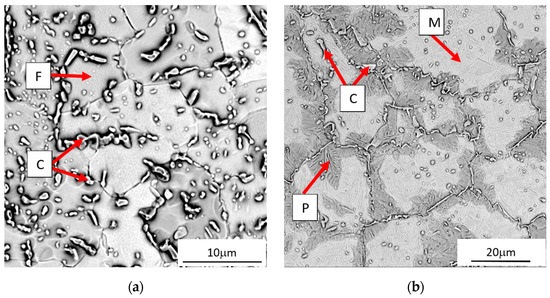
Рисунок 8. Микроструктура стали X46Cr13 ( а ) в монолитной вставке в состоянии поставки (до заливки формы) и ( б ) в составной отливке (после заливки и охлаждения формы); F — феррит, C — карбиды Cr(Fe), P — перлит, M — мартенсит.
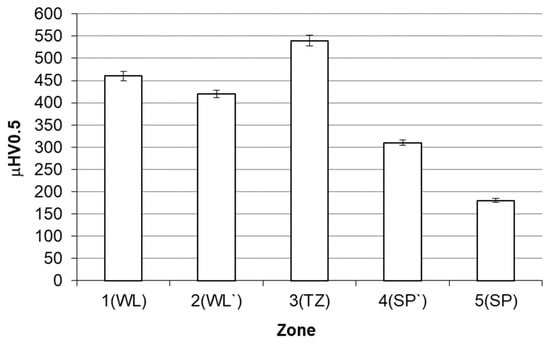
Рисунок 9. Распределение твердости в отдельных зонах составной отливки: сталь X46Cr13–серый чугун EN-GJL-HB 255 (маркировка зон как на рисунке 7 ).
Между зонами 1(WL) и 5(SP) располагаются три переходные зоны. В результате цементации и охлаждения от высокой температуры с умеренной скоростью, т.е. фазовые превращения происходят в твердом состоянии, образуется узкая зона 2(WL`). Поскольку охлаждение зоны от высокой температуры осуществляется с меньшей скоростью по сравнению со скоростью охлаждения для зоны 1(WL), то доминирующей составляющей карбидов Cr(Fe) является перлит, что, в свою очередь, приводит к снижению твердости до уровня 420 μHV0.5.
Другая зона 3(TZ) образуется из жидкой фазы в результате науглероживания приграничной зоны стальной вставки чугуном, что снижает его температуру ликвидуса и солидуса, а затем плавления этой зоны в результате воздействия высокой температуры жидкого чугуна. Химический состав, образующийся в этой зоне, определяет кристаллизацию микроструктуры с конечной твердостью 540 μHV, состоящей из большого количества карбидов Cr(Fe), в основном M7C3 в перлитной матрице ( Рисунок 10 , Рисунок 11 и Рисунок 12 ) .
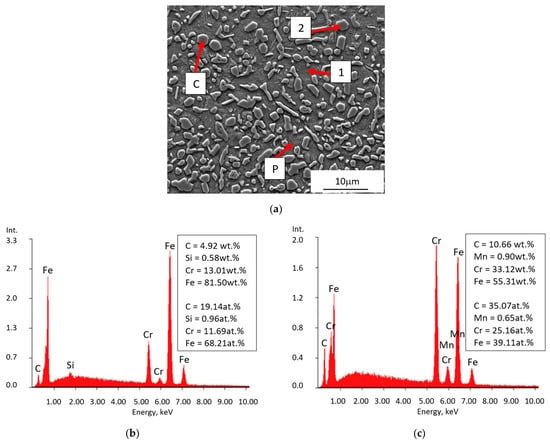
Рисунок 10. Микроструктура зоны 3(TZ) в отливке из сплава сталь X46Cr13–серый чугун EN-GJL-HB 255: ( a ) опытная зона, ( b ) результаты EDS в точке 1 из ( a ), ( c ) результаты EDS в точке 2 из ( a ); P — перлит, C — карбиды Cr(Fe).
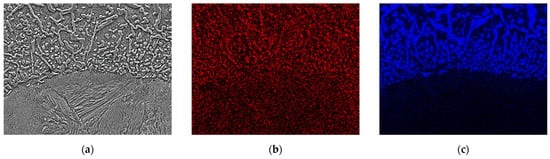
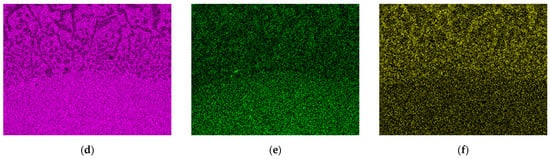
Рисунок 11. Поверхностное распределение элементов на границе зон 3(TZ) и 4(SP`) в составной отливке из стали X46Cr13 и серого чугуна EN-GJL-HB 255: ( a ) опытная зона, ( b ) C, ( c ) Cr, ( d ) Fe, ( e ) Si и ( f ) Mn.
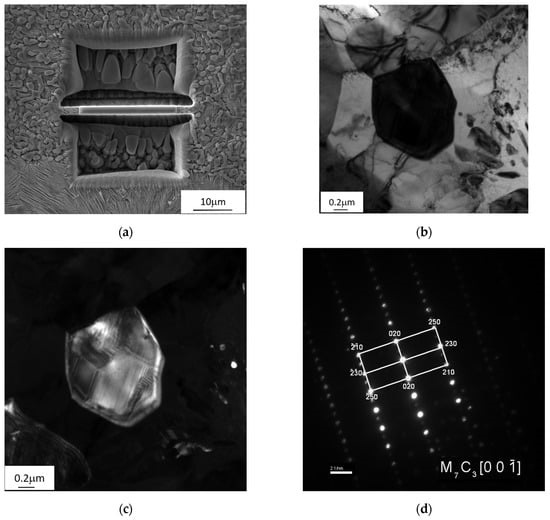
Рисунок 12. Карбид M 7 C 3 в перлите в зоне 3(TZ) в составной отливке из стали X46Cr13 и серого чугуна EN-GJL-HB 255: ( a ) метод взятия пластины из зоны 3(TZ) для испытаний в просвечивающем электронном микроскопе, ( b ) светлое поле, ( c ) темное поле и ( d ) выбранная область электронной дифракции (SAD).
Затем появляется перлитная зона 4(SP`), представляющая собой обезуглероженную микроструктуру опорной части отливки ( рисунок 13 ).
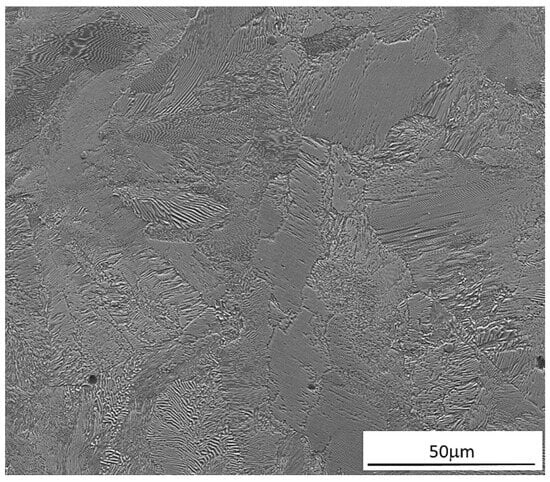
Рисунок 13. Перлитная микроструктура в зоне 4(SP`) в отливке из стали X46Cr13–серого чугуна EN-GJL-HB 255.
На рисунке 14 представлен вид трех биметаллических пластин со средней твердостью поверхности 450 HV5 ± 12 HV5 после использования в условиях эксплуатации коксового тушильного вагона. Для этих пластин и трех контрольных пластин из крапчатого чугуна со средней твердостью поверхности 350 HV5 ± 14 HV5, эксплуатируемых в тех же условиях, были измерены их вес и толщина. Было обнаружено, что биметаллические пластины показали как объемную, так и массовую потерю на уровне, сопоставимом с пластинами, изготовленными целиком из крапчатого чугуна ( рисунок 15 ).
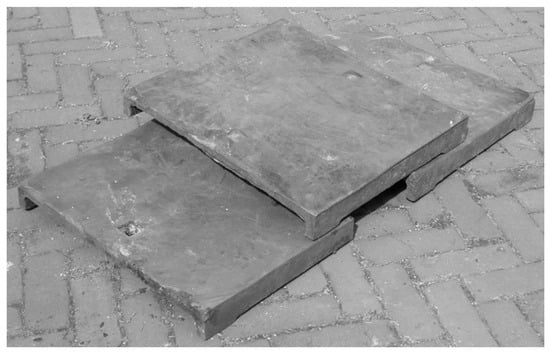
Рисунок 14. Вид трех отливок биметаллических пластин, предназначенных для футеровки вагонов тушения кокса, после завершения 18 500 циклов производства кокса.
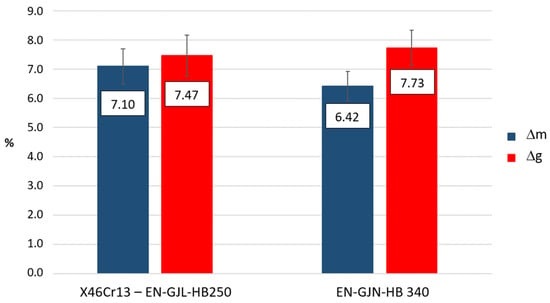
Рисунок 15. Средние потери массы (Δm) и объемные потери (Δg) футеровочных плит коксовых вагонов после завершения 18 500 циклов производства кокса, выполненных из отливок из пористого чугуна X46Cr13–EN-GJL-HB 255 и EN-GJN-HB 340.
Более точные наблюдения показали, что для составных отливок наиболее поврежденные участки располагаются на внешних кромках биметаллического рабочего слоя. Например, на рис. 16 представлен вид фрагмента составной отливки плиты после завершения цикла эксплуатации с видимой, практически полной локальной потерей рабочего слоя из легированной стали X46Cr13. Вероятной причиной представленных повреждений на длинных кромках биметаллических пластин является локальное нарушение контакта между нержавеющей сталью и серым чугуном в условиях многоцикловой термоударной эксплуатации. Это явление приводит к образованию воздушного зазора между рабочим слоем и опорной частью, что увеличивает повреждение в результате ухудшения теплопроводности в циклически нагреваемой и охлаждаемой стальной части и делает возможным попадание воды в зазор, усиливая коррозию. Однако следует отметить, что средняя потеря массы находится на уровне около 7%, при сохранении прочности сцепления практически по всей поверхности контакта в данном типе составных отливок плиты легированная сталь–серый чугун, что определяет ее пригодность для дальнейшего использования в качестве футеровки коксовых вагонов. Дальнейшая пригодность футеровочных плит к использованию является чрезвычайно важным фактором с точки зрения капитального ремонта вагонов тушения кокса. Устранение необходимости демонтажа отдельных плит, обычно выполняемого путем механической резки сильно корродированных крепежных винтов в верхнем положении, позволяет операторам сократить расходы и время капитального ремонта.
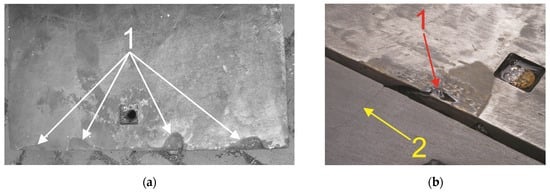
Рисунок 16. Вид повреждения составной отливки (1 на ( а , б )) и трещины в футеровочных плитах отливки из крапчатого чугуна EN-GJN-HB 340 (2 на ( б )) после использования в условиях эксплуатации коксотушильного вагона.
Для отливок из крапчатого чугуна области повышенного повреждения возникают локально, как во внутренних, так и во внешних областях плиты. Кроме того, несмотря на низкую среднюю потерю массы, не превышающую в среднем 6,5%, в одной из анализируемых плит была обнаружена трещина ( Рисунок 16 ). Причиной представленного повреждения термической трещиной плиты из крапчатого чугуна является неравномерное распределение выделений углерода в микроструктуре отливки и преимущество в количестве цементита (повышающего стойкость к абразивному износу) над пластинчатым графитом (повышающего теплопроводность) в перлитной матрице. Наличие сквозной трещины плиты ( Рисунок 17 ) делает ее, в отличие от двух оставшихся, непригодной для дальнейшего использования в качестве футеровки коксовых вагонов. Можно сделать вывод, что сквозная трещина одной из трех плит является частью тенденции, которая сопровождает использование этого чугуна в коксовых вагонах. По нашим наблюдениям, полученным в ходе испытаний, от 30 до 40% чугунных пластин с пятнами повреждаются трещинами до того, как весь вагон выводится из эксплуатации и отправляется на капитальный ремонт.
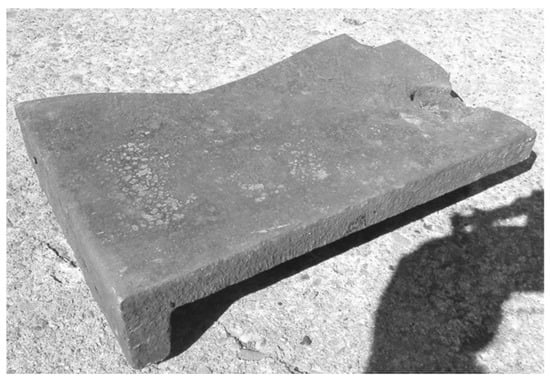
Рисунок 17. Вид поврежденной испытательной футеровочной плиты из крапчатого чугуна EN-GJN-HB 340.
В ходе лабораторных испытаний футеровочных плит коксовых вагонов установлено, что в процессе производства кокса происходит незначительное науглероживание, сульфидирование и фосфатирование рабочего слоя биметаллической отливки ( таблица 2 ). Кроме того, установлено, что снижение концентрации Cr на 0,2 мас.%, при общей концентрации этого компонента более 14 мас.%, можно считать незначительным, например, с точки зрения коррозионной стойкости рабочего слоя биметалла. Аналогично, изменения концентрации других компонентов можно считать менее существенными.
Однако на основании проведенных металлографических испытаний ( рисунок 18 ) установлено, что 18500 выполненных циклов получения кокса практически не вызвали существенных изменений в отдельных переходных зонах составной отливки. Лишь в микроструктуре биметаллического рабочего слоя (зона 1(WL)) по сравнению с исходным состоянием до начала эксплуатации отмечено несколько увеличенное количество перлита за счет мартенсита. В результате твердость рабочего слоя по сравнению с исходным состоянием до начала эксплуатации несколько снижена на 30 HV5, т.е. до уровня 420 HV5 ± 9 HV5. Однако масштаб изменений микроструктуры рабочего слоя и его твердости можно считать пренебрежимо малым, особенно с учетом количества циклов нагрева и охлаждения, которым подвергались опытные отливки.
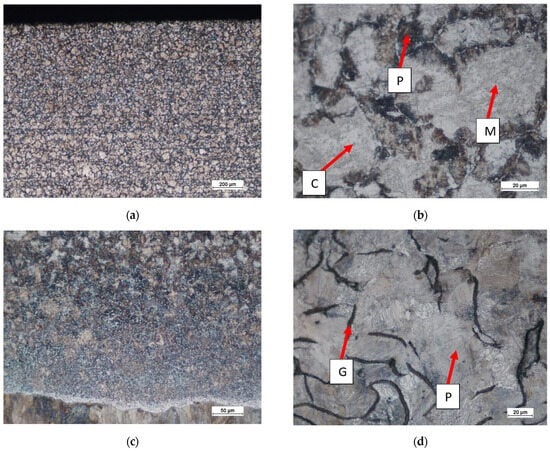
Рисунок 18. Микроструктура отливки футеровочной плиты из сплава X46Cr 13–EN-GJL-HB 255 после эксплуатации в коксотушильном вагоне; ( а , б ) — рабочий слой (зона 1(WL); ( в ) — область сцепления с зонами диффузионного перехода 3(TS)—4(SP`); ( г ) — опорная часть (зона 5(SP); П — перлит, М — мартенсит, С — карбиды Cr(Fe), Г — пластинчатый графит.
Подводя итоги, можно сказать, что в объем проведенных испытаний вошла технология создания составных отливок, состоящих из двух частей: рабочего слоя из высокохромистой стали марки X46Cr13 и опорной части из серого чугуна марки EN-GJL-HB 255, в системе «жидкое – твердое» путем предварительной установки монолитной вставки в полость формы.
Решающее влияние явления диффузии С, показанное в статье, на формирование связи между материалами рабочего слоя и несущего слоя, очевидно, обусловлено фактом легкого переноса компонента по межузельному механизму из одного материала в другой, в отличие от вакансионного механизма, имеющего место, например, для Fe, Mn, Cr, Mo или Ni. Исключение из анализа других компонентов, кроме С, присутствующих в химическом составе как рабочего слоя, так и несущей части, более оправдано, поскольку, несмотря на широкий диапазон концентрационной изменчивости, например, для хрома, результаты проведенных испытаний не показывают заметного количественного влияния на качество связи между обеими частями.
Учитывая это, было установлено, что прочная диффузионная связь между материалами компонентов составных отливок, выполненных в компоновке рабочий слой из легированной стали – опорная деталь из серого чугуна, создается в первую очередь за счет переноса углерода в сторону меньшей концентрации, т. е. от опорной детали к рабочему слою. Поскольку материал опорной детали, выполненной по представленной технологии, заливается в форму, где материал рабочей детали уже помещен в виде стальной пластины, то перенос углерода связан на первом этапе с диффузией в системе жидкость–твердое тело, а после завершения процесса затвердевания – с механизмом диффузии в твердом состоянии. Разумеется, указанные выше диффузионные процессы являются термически активируемыми, поэтому переносу углерода предшествует перенос тепла в том же направлении, т. е. от «горячего» жидкого сплава, залитого в форму, к «холодной» монолитной вставке. Поэтому для получения прочной диффузионной связи по всей поверхности контакта рабочего слоя и опорной детали необходимо использовать достаточно высокую температуру заливки чугуна.
Ход представленных процессов позволяет сделать вывод, что создание прочного диффузионного соединения в анализируемых составных отливках происходит в четыре последовательных этапа:
I этап: Смачивание монолитной вставки жидким чугуном, залитым в форму. На этом этапе необходимо соблюсти условие θ < 90° для контактной поверхности вставки, где θ - краевой угол смачивания, образованный нанесением флюса на контактные поверхности монолитной вставки.
Стадия II: Тепловая диффузия С в направлении от жидкого чугуна к стальной монолитной вставке. На этой стадии мы применяем температурно-концентрационное условие для системы жидкий сплав–вставка:
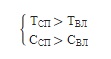
III этап: Оплавление тонкого слоя (до нескольких десятков мкм) на поверхности монолитной вставки, остающейся в непосредственном контакте с жидким сплавом в результате цементации, что снижает температуру ликвидуса и солидуса. Гипотетическое распределение температуры и концентрации углерода в анализируемой биметаллической системе на данном этапе наглядно представлено на рисунке 19 .
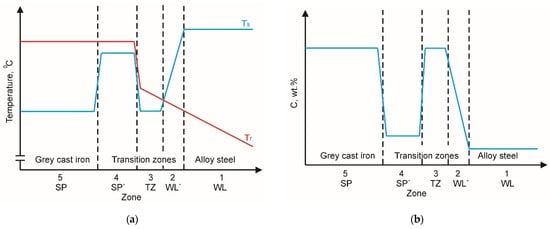
Рисунок 19. Гипотетическая температура ( а ) и концентрация С ( б ) в отдельных зонах структуры составной отливки в период, соответствующий стадии III: T S — температура солидуса, T r — фактическая температура анализируемой биметаллической системы.
Стадия IV: Твердотельная диффузия C. На этой стадии структура составной отливки, сформированная в основном на стадии III, консолидируется и удовлетворяет следующему концентрационному условию:
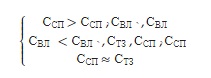
Представленные явления переноса массы и тепла обусловливают формирование составных отливок, где по материальной схеме серый чугун–высокохромистая сталь можно выделить пять основных зон. Последовательно, в направлении от опорной части к рабочему слою, располагаются:
• Зона (SP), соответствующая серому чугуну, используемая для опорной части, содержащей пластинчатый графит в перлитной матрице; • Зона перлита (ЗП`), образованная в приграничной зоне опорной части, создана в результате обезуглероживания, связанного с переносом С в область с меньшей концентрацией, т.е. в рабочий слой; • Переходная зона (ПЗ), состоящая из большого количества карбидов Cr(Fe), в основном M7C3 в перлитной матрице, образованная из жидкой фазы в результате цементации, снижающей температуру плавления приграничной зоны рабочего слоя, и последующего ее расплавления под действием высокой температуры, и полученная в ходе переноса тепла от жидкого сплава к монолитной вставке; • Зона (WL`), образованная в рабочем слое в твердой фазе путем цементации (недостаточной для существенного снижения температуры плавления) и охлаждения от высокой температуры (недостаточной для расплавления этой области), обусловливающая возникновение микроструктуры с карбидами Cr(Fe) в перлитно-мартенситной матрице с преобладающим количеством перлита; • Зона (ЗП) с микроструктурой , образованной в результате самозакалки стали X46Cr13, т.е. карбиды Cr(Fe), в основном M23C6 в мартенситно -перлитной матрице с преобладающим количеством мартенсита. Кроме того, анализ результатов испытаний, проведенных в реальных условиях эксплуатации коксового завода, показывает пригодность составных литых плит в компоновке легированная сталь X46Cr13–серый чугун EN-GJL-HB 255 для использования в качестве футеровки коксовых вагонов. Такие биметаллические плиты характеризуются стабильностью микроструктуры и, как следствие, работоспособностью при циклически переменных процессах нагрева и охлаждения, необходимых в процессе эксплуатации коксового вагона. Учитывая это, благодаря своим потребительским свойствам такие отливки могут успешно заменить плиты, используемые в качестве футеровочных плит для коксовых вагонов до сих пор, полностью изготовленные из низколегированного мелкозернистого чугуна EN-GJN-HB 340. Следует отметить, что себестоимость производства, а следовательно, и закупочная цена биметаллической плиты в рассматриваемой материальной компоновке примерно на 50% выше, чем для цельнолитой чугунной плиты. Наибольшее влияние на себестоимость изготовления биметаллической плиты оказывает цена плиты толщиной 5 мм из высокохромистой стали и стоимость изготовления песчаной формы с учетом представленной в статье процедуры изготовления монолитной вставки. Однако эта стоимость может быть компенсирована более высоким сроком службы биметаллических плит по сравнению с чугунными, что приводит к отсутствию необходимости замены поврежденных (трещиноватых) плит. Таким образом, с одной стороны, обеспечивается экономия за счет отсутствия необходимости закупки новой плиты взамен поврежденной, как уже обсуждалось, а с другой стороны, снижаются и затраты на капитальный ремонт коксотушильных вагонов.
Выводы
На основании анализа результатов испытаний были сделаны следующие выводы:
1. К явлениям, определяющим образование постоянной связи между двумя соединяемыми сплавами, являющимися составными материалами составной отливки, относятся перенос тепла и углерода в направлении от «горячего и высокоуглеродистого» материала опорной части, залитой в форму, к «холодному и низкоуглеродистому» материалу рабочего слоя, размещенного в виде монолитной вставки внутри полости формы. Таким образом, процесс образования постоянной связи между рабочим слоем и опорной частью в представленной технологии составного литья происходит последовательно в результате смачивания контактной поверхности монолитной вставки жидким сплавом, залитым в форму, а затем путем термически активированной диффузии углерода в системе жидкий сплав–вставка.
2. Важнейшим аспектом формирования постоянной диффузионной связи между двумя сплавами в представленной технологии получения композиционного чугуна было создание условий для возникновения переходной зоны путем цементации материала для снижения температуры ликвидуса и солидуса и последующего расплавления тонкого слоя стальной монолитной вставки, остающейся в непосредственном контакте с жидким чугуном, залитым в форму.
3. Использование литья из смеси легированная сталь X46Cr13–серый чугун EN-GJL-HB 255 взамен применяемого в настоящее время для литья футеровочных плит коксотушильных вагонов коксогазового назначения позволяет продлить срок службы деталей, прежде всего за счет их более высокой стойкости к растрескиванию.